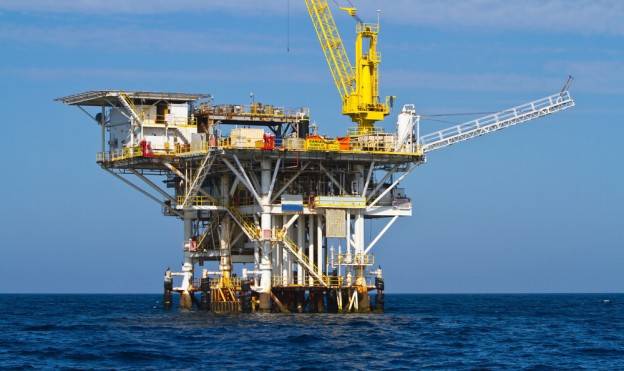
The onshore deposits of oil and gas are depleting with each passing year and it prompts people to seek new energy sources. Exploration and development of oil and gas from offshore deposits gives modern society the possibility to extend into the time when some other form of fuel will be able to replace oil and natural gas.
Offshore drilling is performed on special platforms, floating or semi-submerged drilling rigs. The term “offshore drilling” was first used in 1869 when the project of a drilling rig for shallow-water operations was first patented in the USA. Since that time, science has not remained idle. So today we have mobile rigs that can be operated at the depth of between 300 meters and 3 kilometers. If the drilling is performed on these offshore platforms, they use special electrically-operated rigs that are powered by cable lines of 6 and 35 kW. Single-motorized rigs are used when drilling from individual offshore platforms. As a rule, floating semi-submerged platforms are equipped with diesel-electric drives to produce AC and DC current.
The number of machines, their capacity and the capacity of the driving engines of the main and additional units depend on the drilling depth and the sea depth.
An electric power transformer is an integral part of offshore drilling since it provides power for drilling platforms, converting the AC voltage into the voltage needed by the equipment it is servicing. So, it is the electric power transformer that helps to determine the reliability and efficiency of the drilling rigs as well as the whole offshore drilling process.
Transformer oil in the power transformers is necessary to transfer heat and insulate the current-conducting parts from non-conducting parts. During operations, insulating oil is exposed to a wide range of unfavourable factors that contribute to the degradation of its performance characteristics. That is why oil needs reclamation on a timely basis to maintain its physical and chemical characteristics at the desired level.
When operated, drilling rigs are exposed to the risk of explosion. The equipment used on offshore drilling platforms therefore, should come in an explosion-proof design. This is also true for the equipment used for transformer oil reclamation.
GlobeCore is one of the leading manufacturers of oil purification and regeneration equipment. One of GlobeCore’s latest developments is the Clean Marine Unit specifically designed for transformer oil recycling/regeneration/reclamation on offshore drilling platforms. It is explosion proof and protected from saltwater moisture and corrosive materials.
The Clean Marine Unit is used to degas and purify transformer oil by removing mechanical impurities and by vacuumizing transformers in the offshore industry.
The GlobeCore Clean Marine may be operated in one of the following modes:
(1) transformer oil heating; (2) oil degassing; and (3) vacuumizing.
GlobeCore equipment, designed for offshore platforms, restores the performance characteristics of insulating oil, extends its service life and increases the reliability of electric power transformers.