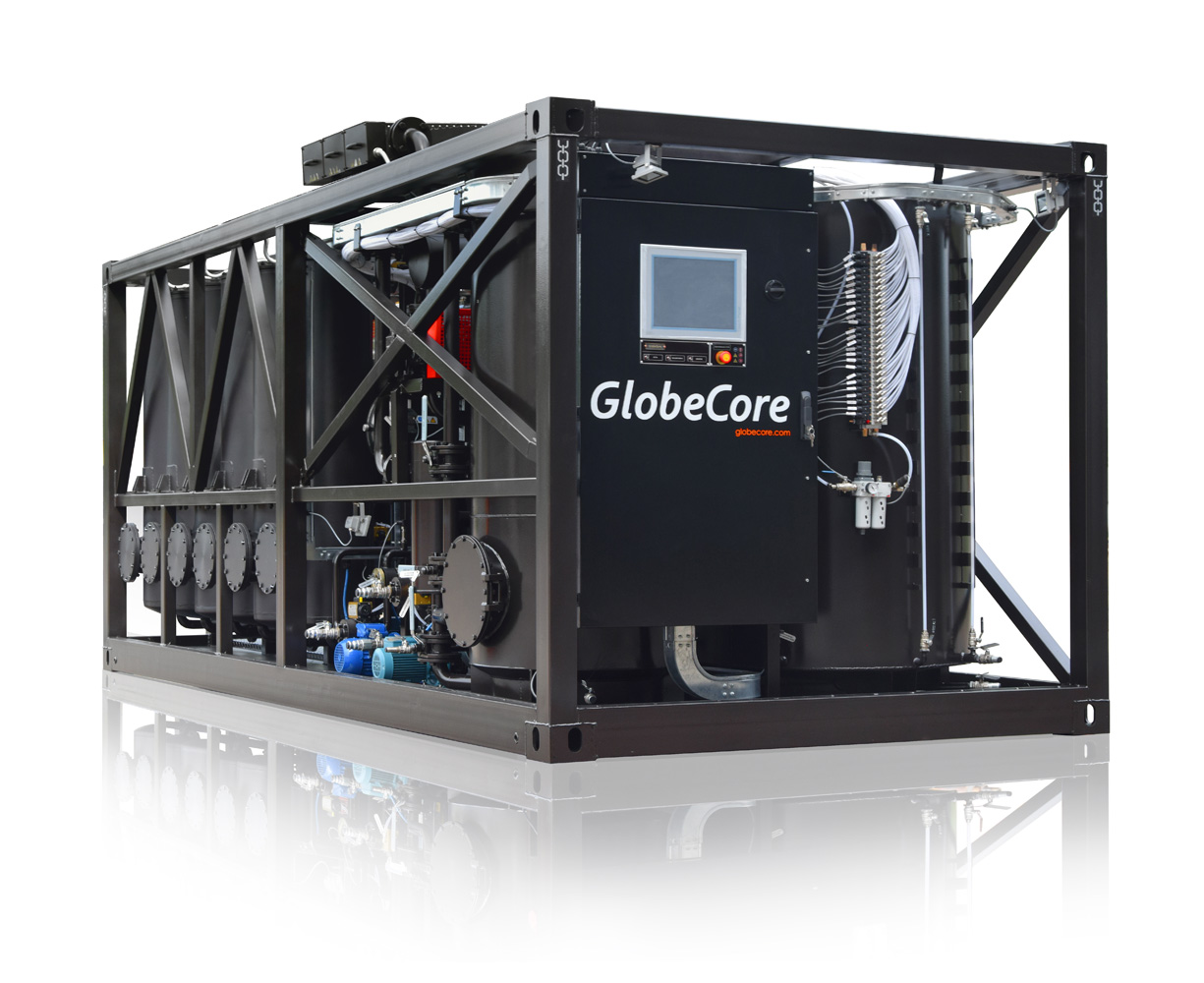
In practical terms, transformer oil oxidation is caused not only by contact with atmospheric air but also by gases that become dissolved in the oil. Oxidation is not the only negative after-effect of this process. Dissolved gases and gases, found in the solid transformer insulation, reduce the dielectric strength of the insultaion system made of both liquid and solid parts. The oxidation is caused by the fact that occluded gas becomes the source for the development of unwanted electric charges.
The issues of oil degassing and transformer vacuumizing have taken on enormous importance since transformers with a higher voltage became widely used in the electric transmission industry. The rate of saturation of oil with gases is determined by the height of the oil column and the contact surface with gas. The rate of the reversing the process depends on the same parameters.
Vibration may lead to the formation of bubbles in oil, caused by depression zones. This tends to have an adverse effect on the insulating system’s reliability. That is why vibration of energized transformers should be reduced to a minimum. In practice, special units, called “columns” are used to perform vacuumizing. There is a screen inside a column equipped with atomizers.
To provide the highest level of efficiency, these atomizers should have the largest possible area per unit of volume and the least possible resistance to the oil flow. The most appropriate atomizers are considered to be a set of devices called “Raschig Rings.” They are similar in appearance with rings, the diameter of which equals its height. Such rings may be made of different materials such as metal, porcelain, and ceramics.
In practical terms, electric utilities use GlobeCore CMM-R units for transformer oil degassing. They are designed to remove gases, mechanical impurities and to heat up transformer oil found in transformers with a voltage of up to 1150 kW. In addition, such equipment may also be used to heat up oil-filled electrical equipment and to dry and vacuum transformers.
The following are the parameters of processed oil:
- gas content, %, no more than 0.1;
- mass moisture content, g/t, no more than 5;
- ISO 4406 purity class – 9.