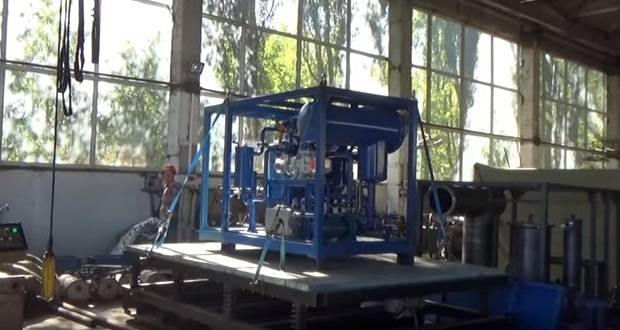
GlobeCore is one of the leading manufacturers and suppliers of industrial equipment designed for use in the road building (road bitumen emulsion and modified bitumen production) and electricity industries (power transformer oil reclamation and oil purification).
It is impossible to take the lead in any kind of activity without the full consideration of the needs of the customer. Today, sales of GlobeCore equipment covers more than 70 countries located all over the world.
During the transportation and delivery of industrial equipment, equipment is exposed to many negative factors, among which a special place belongs to harsh vibration. Vibrations are essentially mechanical oscillations transmitted from the source of the vibration to the industrial equipment. If the delivery to the Customer is done by air, the vibration sources may come from the rotation of high speed rotors found in jet engines and propellers, and from air vortices and the pulsations from turbulent airflow.
Vibration can also take place when industrial equipment is transported by sea. Most often it is caused by the blows of waves against the hull of the transport vessel, but the operation of the propeller, internal combustion engines, turbines, and electric motors can cause vibrations. Transporting by road is also not free from vibrations that can harm industrial equipment.
When designing and manufacturing industrial equipment, vibration protection and testing are integral parts of the quality control program. A good comprehensive testing program will also include temperature tests and tests for moisture resistance. In order to ensure long term product quality and durability, GlobeCore’s units are exposed to a certain level of vibration in accordance with manufacturing and testing procedures defined by strict international standards.
In order to create certain types of vibration, GlobeCore uses special activators known as shakers that convert electrical signals into mechanical motion. The shakers are capable of maintaining the vibrations at the desired vibration levels for the full duration of the testing process.
Before and after the testing, critical measurements are taken that include:
- airtightness;
- productivity;
- pressure at the sensors;
- noise level;
After the testing is completed, GlobeCore technicians determine whether the equipment is fit for sale and can be certified as meeting all operational requirements. The conduct of vibration testing helps ensure the full compliance of GlobeCore’s products to their intended purpose. Customer confidence and satisfaction is one of the main priorities of our Company.